There are so many different types of project management techniques that it can be hard to keep track of them all! Lean project management is one of the most popular methodologies, but it isn’t right for every team and for every project.A lean approach can be applied to tech projects such as software development, but it can also be used for manufacturing physical products or even running a meeting. The main focus is on eliminating waste and providing the most value to the customer.Let’s take a look at the principles of lean project management and how it compares to other methodologies such as agile project management.
What is lean project management?
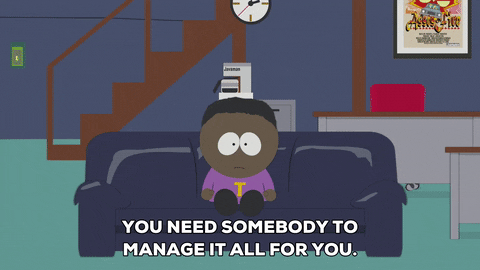
Lean project management is based on the lean manufacturing process first developed in Japan. At its core, the lean methodology is about reducing waste – both in the form of labor as well as physical materials, including equipment and work space.The lean approach is still used at Toyota Motor Corporation today, and you can find some of the key Japanese phrases in the Toyota Production System (TPS) glossary. The three core principles to keep in mind are muda, muri, and mura:
- Muda means “waste” and covers everything from unused stock and storage space to manufacturing defects and transportation costs.
- Muri means “overburden” and can be applied to both employees or machinery and equipment. (Pulling all-nighters to meet a deadline? That’s muri.)
- Mura translates as “unevenness” and refers to things like production delays and backlogs. Reducing unevenness can improve overall productivity.
The goal of lean project management is to eliminate all three types of waste and cut down on bottlenecks, overproduction, and other inefficiencies.By following lean management principles, you’ll be better able to meet the needs of stakeholders and improve efficiency across your project team.
The history of lean project management
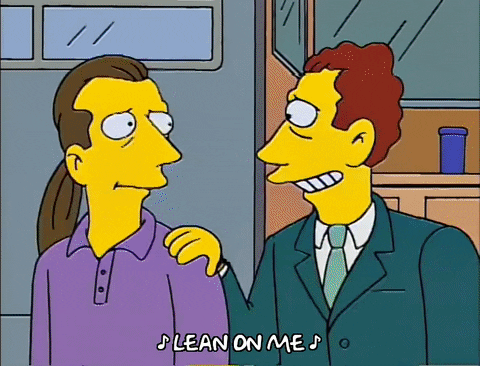
Before we go any further, it’s worth knowing a little more about where lean project management originated and why some project managers swear by it.The lean approach was basically a response to the mass production process that defined manufacturing for much of the 20th century.Mass production is all about making large quantities of products, which can result in unnecessary expenses due to overproduction and storage. Plus, it can be harder to shift gears and make changes to the production line at short notice.In the 1970s, waste became a serious concern due to the energy crisis, and Toyota took steps to address the issue by developing new manufacturing principles.Instead of maximizing output regardless of demand, Toyota switched to a “just-in-time” approach that focused on value stream mapping and customer satisfaction.The company also introduced the concept of kaizen, or continuous improvement, in which work processes are standardized but are re-assessed with every iteration – usually defined as a period of product developmentThese days, lean thinking has spread well beyond Toyota and is a key principle in agile methodology and other software development techniques.
How to use lean project management

Now that we know a little bit about where lean project management comes from and what it’s for, how do you go about introducing it to your project?Basically, you’ll need to follow the five core principles of the lean methodology:
- First, understand value from the customer’s point of view. This means determining what the customer wants and what they’re willing to pay for it. You’ll need to get clear on their requirements and acceptance criteria.
- Second, determine the value flow. This step is referred to as value stream mapping and can be done using a Kanban board, which is basically a modified to-do list made up of movable cards or tasks. You’ll end up with a map that shows every step of the production process.
- Next, develop a continuous flow and make sure every step of the process adds value. This is where you’ll focus on reducing mura, or unevenness, as well as muda – any steps that slow the process down or don’t add value.
- Implement a pull system to align with customer demand. Here’s where the “just-in-time” system comes in. Instead of anticipating what a customer wants and when they’ll want it, lean project management lets the customer call the shots. This eliminates over-production and product surpluses.
- Finally, make continuous improvement a key part of your process. This means that nothing is set in stone and everything gets reassessed to see if it can be streamlined any further. Lean project management isn’t about finding the perfect process but improving it with each iteration.
Lean project management vs. Agile product development
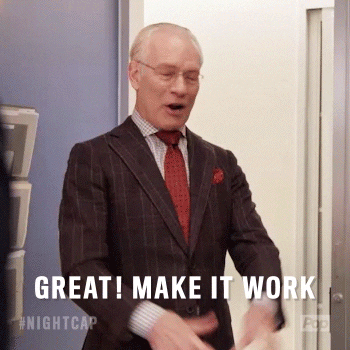
There’s a lot of overlap between different lean project management techniques, and sometimes it can be hard to tell where one ends and another begins. For example, Agile and lean project management are often discussed interchangeably.How different are they, really? In short, Agile is a lean methodology that’s adapted to software development and is designed to be implemented quickly. It can be used for a single project or team without requiring buy-in from the whole organization.Lean project management is a much broader approach that’s designed for long-term planning and should be rolled out through an entire company.Ultimately, though, you can pick and choose the parts of lean project management that work for you. Here are a few more project management tools you can use to improve productivity in your workplace:
- Deming Cycle: Edward Deming was one of the consultants who first helped to bridge the gap between American and Japanese production methods. His big contribution was the Deming Cycle, a four-part process that’s also called the Plan, Do, Check, Act (PDCA) Cycle. You can move through each step during the product development process in a cycle of continuous improvement.
- Lean Six Sigma: This methodology incorporates six steps instead of the four found in the Deming Cycle. While reducing waste is still a part of the process, the emphasis is on reducing variation and improving consistency.
- Kanban: Kanban boards can be used in a wide range of projects and are a handy way to visualize each step in the workflow. Team members can track their progress by moving cards between the “To Do,” “Doing”, and “Done” section of the board, making it easy for you to identify inefficiencies.
These lean tools are just the basics of how the lean methodology works. Full books have been written about the topic, so we can’t do everything justice in a single blog post!Still, by implementing these core principles – and focusing on functionality, customer value, and process improvement – your team will be able to save time, cut down on waste, and reach your project milestones faster.
Use Anchor AI as part of lean project management
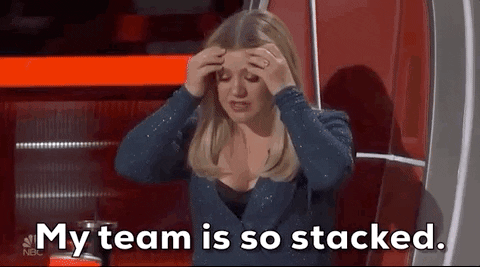
Lean project management is a great choice for teams that want to cut down on wasted time, effort, and materials during software or product development. But for some teams, other techniques like Agile or Kanban methodologies may be a better fit.No matter which project management methodology you choose, Anchor AI can help you streamline your workflow by taking notes and transcribing team meetings.Not only will you end up with a searchable, time-stamped record of everything on the agenda, Anchor AI’s automated notetaking tool can identify which team members are speaking and make note of any action items that you need to follow up on.It’s the perfect addition to the project management process because it saves time and reduces errors throughout the project lifecycle.Learn how to invite Anchor AI to your next team meeting, or sign up today to try it out!