Most of us don’t get things exactly right the first time around — and that’s just as true for businesses as it is for individuals. Sometimes a process turns out to be more expensive or time-consuming than you expected it to be, and you need a system in place to get to the root cause of the problem and create a new process or workflow.Process improvement methodologies help by providing you with a tried-and-true way to identify inefficiencies in your existing processes and optimize them. Let’s take a look at 9 process improvement methods and how to decide which one is right for you.
What Is Process Improvement?
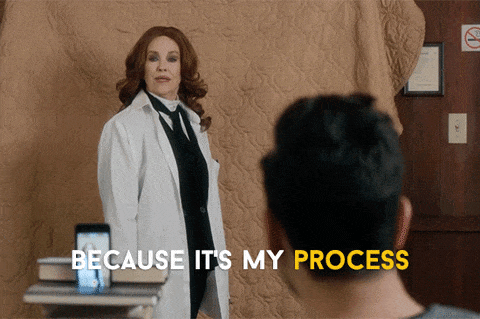
Process improvement is exactly what it sounds like: a way to improve your systems or workflows, usually by eliminating errors, waste, or unnecessary steps. This isn’t just a process of trial-and-error, though: before making any changes, you’ll want to analyze your current processes to find inefficiencies, bottlenecks, and redundancies.Process improvement is a data-driven process that requires close observation of key performance indicators and other business metrics to help with problem-solving and decision-making. Using a business process improvement methodology gives you a framework for creating and carrying out your improvement initiatives.
What Are the Benefits of Process Improvement?
Process improvement can benefit many areas of your business, from manufacturing to sales to HR. Almost any process that includes multiple steps or stakeholders is a good candidate for process improvement. Want to develop successful project management strategies? No problem. Need to run more efficient virtual meetings? That too.When used wisely, process improvement methodologies can help you to:
- Increase productivity: By removing unnecessary tasks from your workflow, your team members will get more done in less time. You can even use automation to streamline routine tasks like data entry, transcription, and note-taking.
- Eliminate waste: Although reducing waste is more relevant for companies with a physical product, SaaS businesses and remote teams can benefit from reducing waste too. Save on virtual storage space or computer hardware by streamlining your workflows so they use fewer resources.
- Reduce expenses: Process improvement can help to increase profitability if your new processes take less time or have reduced operating costs.
- Improve quality: Streamlined processes can result in higher-quality outputs with fewer mistakes due to mechanical failures or human error.
Process improvement can also result in faster time to market, or a more nimble product cycle, to help you stay competitive and improve customer satisfaction.
9 Process Improvement Methodologies
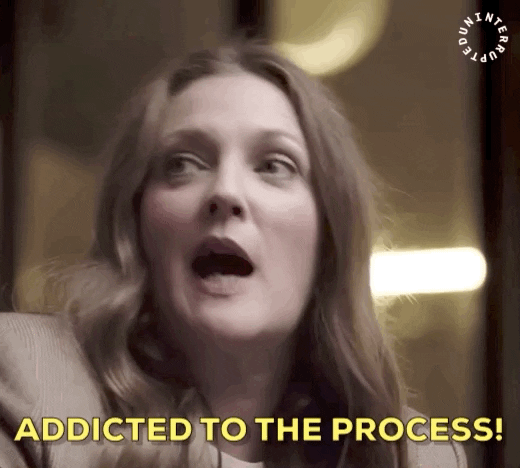
Process improvement methodologies vary in their purpose, timeframe, and complexity. Here are 9 process improvement techniques that may be right for your team:
1. Six Sigma
Six Sigma has its roots in manufacturing companies like Motorola and General Electric. It’s a diagram-based methodology that uses an Ishikawa diagram or fishbone diagram to help you locate the cause and effect of a problem.The Six Sigma Methodology has two main subsets:
- DMAIC (Define, Measure, Analyze, Improve, Control) for existing processes
- DMADV (Define, Measure, Analyze, Design, Verify) for new processes
You can also use a SIPOC analysis diagram to analyze your Suppliers, Inputs, Process, Outputs, and Customers, and look for opportunities for improvement.
2. Lean Manufacturing
While Six Sigma is all about eliminating defects, the lean methodology is primarily used as a way to cut down on waste. It uses process improvement techniques such as value stream mapping and quality control in order to implement change.Lean manufacturing has some similarities with the Toyota Production System (TPS) and the “just-in-time” manufacturing process. Rather than continuously producing a product and running the risk of overproduction, the lean method relies on the concept of “pull,” or letting customer demand drive the manufacturing process.
3. Total Quality Management (TQM)
Total Quality Management (TQM) is a continuous process improvement methodology, which means it doesn’t happen just once, but on an ongoing basis.TQM is all about the customer experience. You’ll focus on delivering the level of quality that customers want by ensuring that your employees are able to meet clearly defined standards and expectations.
4. PDCA Cycle
The PDCA Cycle contains four steps: Plan, Do, Check, and Act. Because it’s a cycle, this approach is also a continuous improvement tool, and can be used as part of the TQM process. You’ll start by making a Plan, testing it out (Do), Checking the results, and either Acting on it or not, depending on the outcome.This way, you don’t have to overhaul your entire workflow on an unproven process. By checking the results each time you make a change, you can decide whether to move forward with the process or to dial it back.This approach is also called the Deming Cycle after its creator, and there are several variations that make it suitable for a wide range of industries.
5. Kanban
The Kanban method is one of the most popular process improvement methodologies out there. You’ve probably seen it in action if you’ve ever used project management tools like Asana or Trello, which use Kanban boards to keep track of tasks.The Kanban method got its start as a process improvement technique at Japanese manufacturing companies like Toyota, but now it’s used around the world. Kanban boards are especially useful for providing a visual representation of a process.
6. Kaizen
The Kaizen methodology is another Japanese method that revolves around three key concepts: wastefulness (Muda), overproduction (Mura), and overburden (Muri).This is a continuous improvement process that helps you stay aware of potential pitfalls in these three problem areas. Are your employees overworked? Are you producing too much waste or too much product?The Kaizen philosophy isn’t about a one-time, radical change to your existing systems, but about ongoing incremental improvements.
7. Process Mapping
Process mapping is a great way to visualize an existing process so you can easily see any inefficiencies or redundancies. Process maps usually take the form of a flowchart, with arrows showing the direction of movement between each step or action.Use this method to help stakeholders get a clear grasp of their role in a project, or to assess the scope, time, and cost of a project before you begin.
8. Theory of Constraints
The Theory of Constraints is a problem-solving strategy that can help you identify where things are getting held up along the way. In this case, the focus is on isolating a specific problem or constraint and improving the process until you’ve eliminated it.As with process mapping, you can use a diagram to help you visualize bottlenecks and redundancies and get to the root cause of an issue.
9. Business Process Management (BPM)
Business Process Management (BPM) is broader than some of the other methodologies on our list, because it encompasses everything from process modeling to automation.The core goal here is efficiency: You’ll be looking for bottlenecks in your workflow, such as repetitive tasks that you can automate or redundant tasks you can eliminate.While some methodologies are designed for physical manufacturing, BPM is a good fit for software companies because of its focus on automated workflows.
How to Choose the Right Process Improvement Methodology
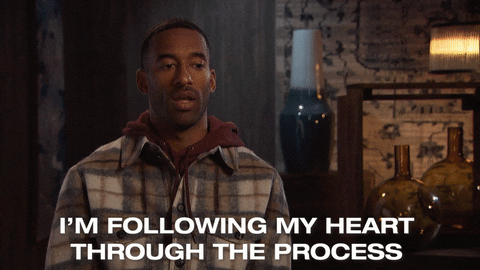
The best process improvement methodology for you will depend on the current state of your business and your end goal. Each methodology has its own area of emphasis, but there’s a lot of overlap between these methods, and some of them can be combined or even used interchangeably.For example, Six Sigma is focused on defects and lean manufacturing is focused on waste, but you can combine the two into the Lean Six Sigma Methodology. Or, you can use one of the diagrams mentioned above (such as a process mapping flowchart or a PDCA cycle template) as part of the Total Quality Management (TQM) process.Try not to overthink it: The important thing is to find a method that allows you to think clearly about a process and identify areas for improvement. If one methodology isn’t right, move on to the next one until you find a good fit.
Streamline Manual Processes With Anchor AI
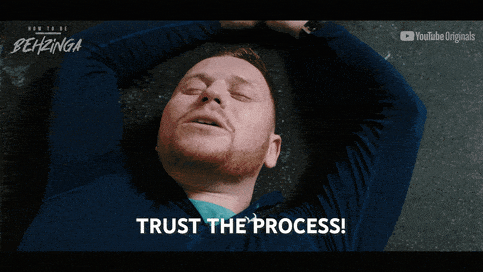
Process improvement methodologies can save your organization time and money by reducing waste and improving efficiency. But no matter which process improvement methodology you choose, it’s important to track your progress and take notes.Anchor AI makes it easy to get more done during the improvement process. Not only can our AI-powered tool transcribe your meetings, it can also identify action items and generate meeting minutes. By automating the note-taking process, you’ll be able to reduce manual labor and eliminate bottlenecks along the way.Sign up for free today to test it out and see just how efficient your meetings can become.